Addressing Challenges In Automated Visual Inspection Of Lyophilized Vials
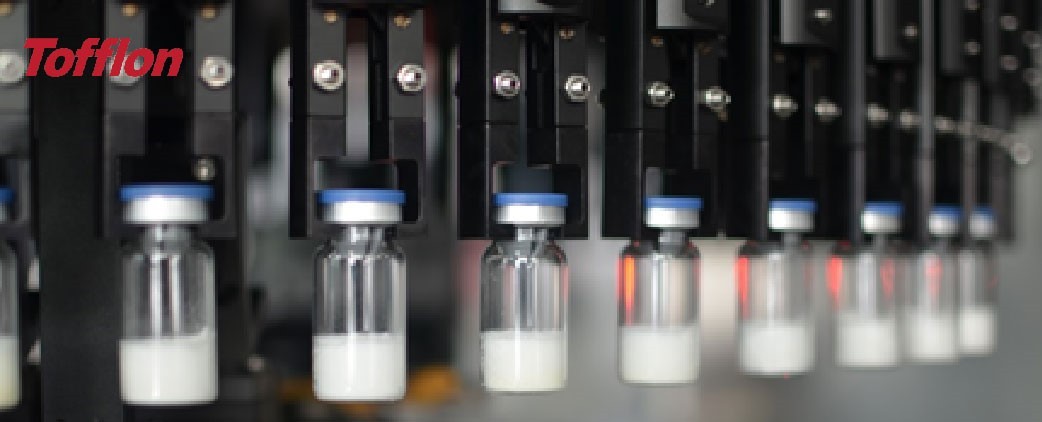
Table of Contents
Challenges Posed by Lyophilized Vial Characteristics
The physical characteristics of lyophilized vials introduce significant complexities to automated visual inspection. The seemingly simple task of identifying defects becomes considerably more difficult due to several factors.
Variability in Cake Appearance
The appearance of the lyophilized cake itself is highly variable. Cracks, fissures, collapse, and inconsistencies in the cake's surface are common occurrences. This variability makes it challenging to establish consistent acceptance criteria for automated systems.
- Examples of visual defects: Surface cracks, partial collapse, fissures, uneven surface texture, discoloration.
- Impact on drug product quality: These defects can compromise the stability and sterility of the drug product, leading to potential efficacy issues and safety concerns.
- Difficulty in algorithmic detection: The subtle nature of some defects and the wide range of acceptable variations make algorithmic detection challenging, often leading to false positives or missed defects.
- Solutions: Advanced image analysis algorithms, including machine learning and deep learning models trained on large datasets of images with various defects, are necessary to handle this variability effectively. These algorithms can learn to differentiate between acceptable variations and critical defects.
Light Scattering and Reflections
Light scattering and reflections from the vial surface and the lyophilized cake are major sources of interference in AVI. These reflections can mask actual defects, leading to inaccurate inspection results.
- Types of lighting used in AVI: Various lighting techniques, including diffused, coaxial, and structured lighting, are employed in AVI systems. However, each has limitations in handling reflections from lyophilized vials.
- Strategies to minimize light scattering: Careful optimization of lighting angles, polarization filters, and advanced imaging techniques are crucial to mitigate these issues.
- Impact on image quality: Scattered light reduces image contrast and clarity, hindering the ability of the automated system to accurately identify defects.
- Potential solutions: Specialized lighting techniques, such as structured illumination microscopy, combined with advanced image filtering algorithms can significantly improve image quality and reduce the impact of light scattering and reflections.
Vial-to-Vial Variation
Inconsistencies in vial clarity, color, and surface finish are another major challenge. These variations can affect the accuracy of defect detection and necessitate robust calibration procedures.
- Sources of vial-to-vial variation: Variations in glass manufacturing, cleaning processes, and filling techniques can contribute to inconsistencies in vial characteristics.
- Impact on defect detection: Variations in vial properties can be misinterpreted as defects by the inspection system, leading to increased false positives.
- Calibration and standardization techniques: Regular calibration and standardization procedures are crucial to ensure consistent performance and minimize errors caused by vial-to-vial variations.
- Machine learning solutions: Machine learning algorithms can be trained to account for these variations and improve the accuracy of defect detection.
Technological Limitations in Automated Visual Inspection Systems
Even with sophisticated algorithms, technological limitations in AVI systems hinder the accurate inspection of lyophilized vials.
Resolution and Sensitivity Limitations
Detecting subtle defects in lyophilized vials requires high-resolution imaging systems. However, achieving sufficient sensitivity without generating a high rate of false positives presents significant challenges.
- Pixel resolution requirements: High pixel resolution is essential to capture fine details and accurately identify small defects.
- Impact of image noise: Noise in the images can interfere with defect detection and increase the rate of false positives.
- Advanced sensor technologies: Advanced sensor technologies, such as CMOS and CCD cameras with high dynamic range, are necessary to capture high-quality images with minimal noise.
- Solutions: Implementing higher-resolution cameras and advanced image processing algorithms, including noise reduction techniques, is crucial to address these limitations.
Software and Algorithm Development
Developing robust algorithms capable of accurately identifying defects while minimizing false positives and false negatives is a complex and ongoing process.
- Challenges in algorithm training: Training algorithms requires large, high-quality datasets of images containing a wide variety of defects.
- Data sets required: Acquiring and annotating these datasets is a time-consuming and labor-intensive task.
- Ongoing algorithm optimization and improvements: Algorithms require continuous optimization and improvement to maintain accuracy and adapt to changing conditions.
- Machine learning and deep learning: Machine learning and deep learning techniques offer significant potential for improving the accuracy and efficiency of defect detection algorithms.
Integration and Validation
Integrating AVI systems into existing manufacturing lines and validating their performance according to regulatory requirements (e.g., 21 CFR Part 11) presents significant logistical and technical challenges.
- Validation protocols: Rigorous validation protocols are necessary to demonstrate the accuracy and reliability of the inspection system.
- Regulatory compliance: Compliance with regulatory requirements is critical to ensure the acceptability of the inspection data.
- System integration challenges: Integrating AVI systems into existing manufacturing lines requires careful planning and execution to avoid disrupting production workflows.
- Importance of validation: Proper validation and compliance are essential to ensure the reliability and trustworthiness of the inspection process.
Strategies for Improving Automated Visual Inspection of Lyophilized Vials
Several strategies can significantly improve the accuracy and efficiency of automated visual inspection of lyophilized vials.
Advanced Image Processing Techniques
Cutting-edge image processing techniques enhance image quality and improve defect detection accuracy.
- Specific techniques: Noise reduction, edge detection, pattern recognition, and image segmentation algorithms play crucial roles.
- Benefits of these techniques: These techniques improve image clarity, highlight defects, and enable more accurate classification.
Machine Learning and Artificial Intelligence
Machine learning (ML) and artificial intelligence (AI) are transforming the field of automated visual inspection.
- Specific AI applications: AI-powered systems can learn to identify subtle defects, reduce false positives, and automate the training process for new algorithms.
- Advantages of using AI: Improved accuracy, reduced human intervention, and faster processing times.
- Limitations: Requires large datasets for training and may require ongoing maintenance and updates.
Improved System Design and Hardware
Advancements in lighting, cameras, and robotic handling systems enhance the accuracy and efficiency of the inspection process.
- Examples of hardware improvements: Higher-resolution cameras, improved lighting systems, and more precise robotic handling mechanisms.
- Impact on the system’s performance: These improvements lead to faster inspection times, higher accuracy, and reduced operational costs.
Conclusion: Ensuring Quality and Efficiency in Automated Visual Inspection of Lyophilized Vials
Automated visual inspection of lyophilized vials presents significant challenges due to the inherent variability of the product and limitations in current technology. However, advanced image processing techniques, machine learning, and improvements in system design and hardware offer promising solutions to overcome these hurdles. Implementing robust strategies for automated visual inspection of lyophilized vials is crucial for maintaining product quality and meeting regulatory standards. Learn more about advanced solutions to enhance your automated visual inspection processes today!
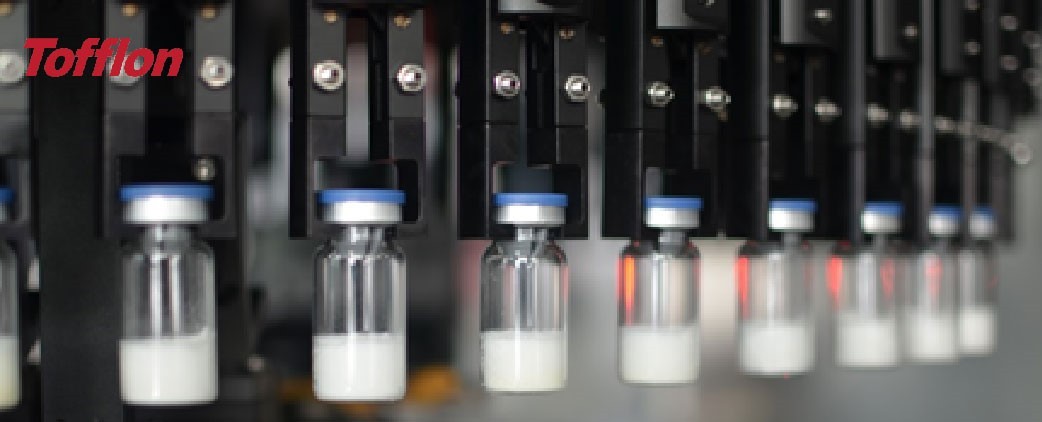
Featured Posts
-
The Next Papal Election Key Cardinals To Watch
May 11, 2025 -
Seattle Businesses Woo Canadian Sports Fans With Par Exchange Rates
May 11, 2025 -
Analiza Veniturilor Lui Sylvester Stallone Din Seria Rocky
May 11, 2025 -
Payton Pritchards Game 1 Performance Key To Celtics Playoff Success
May 11, 2025 -
Is A Crazy Rich Asians Tv Show Really Happening Updates And News
May 11, 2025