Can America Fill The Restored Manufacturing Jobs? A Look At The Workforce
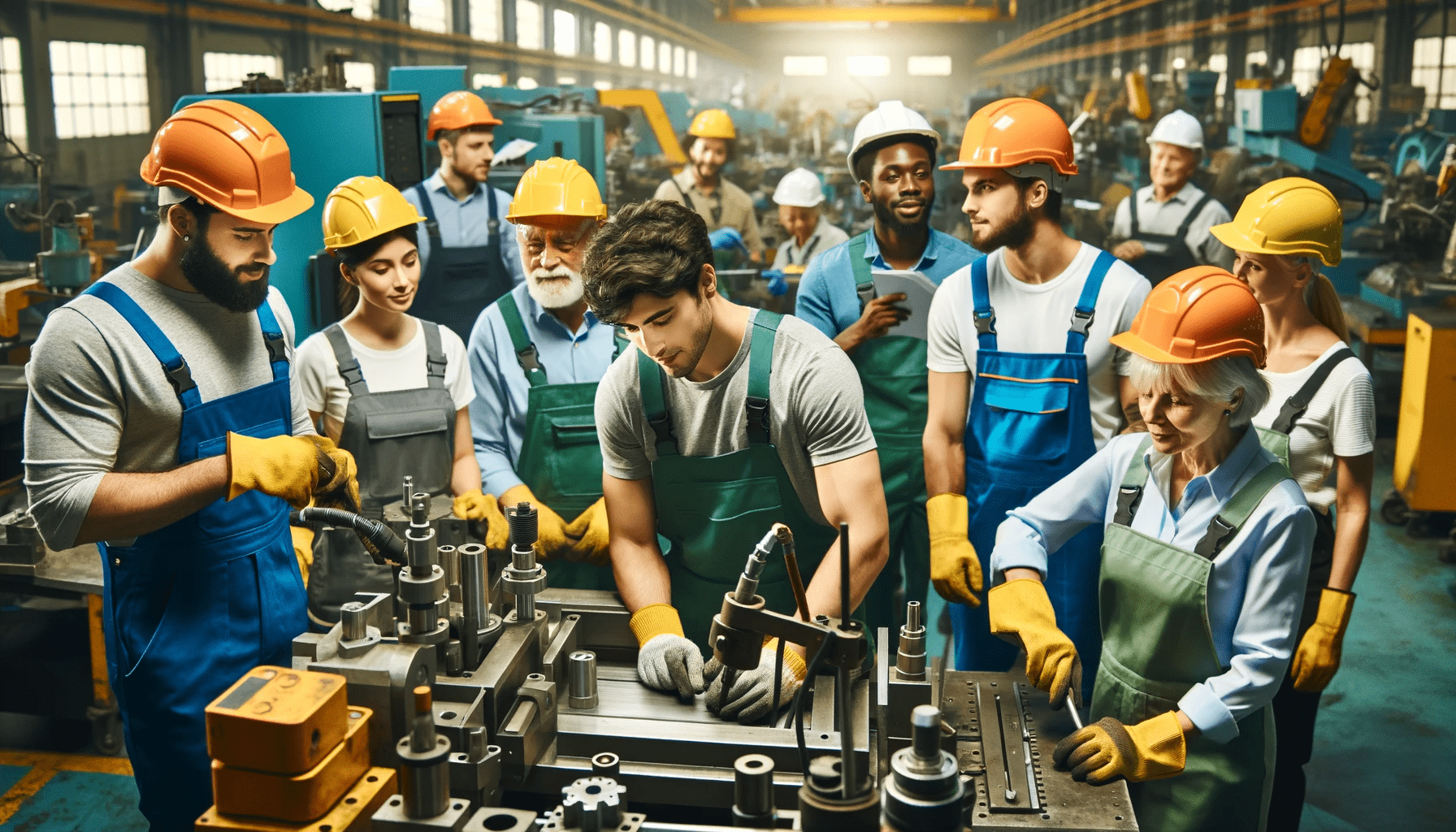
Table of Contents
The Skills Gap in Restored Manufacturing
The modern manufacturing landscape is vastly different from its past. It demands a highly skilled workforce proficient in advanced technologies, creating a significant skills gap. This mismatch between available worker skills and employer needs poses a major hurdle to the growth of the restored manufacturing jobs sector.
Demand for Specialized Skills
The jobs of today's factories require expertise beyond basic manual labor. Modern manufacturing relies heavily on automation, advanced robotics, data analytics, and sophisticated machinery. This necessitates a workforce with specialized skills.
-
Examples of In-Demand Skills:
- CNC machining and programming
- PLC (Programmable Logic Controller) programming and troubleshooting
- Industrial robotics maintenance and programming
- Data analysis for quality control and process improvement
- Mechatronics and automation system integration
- 3D printing and additive manufacturing techniques
-
Statistics Highlighting the Disparity: According to recent reports from the Manufacturing Institute, hundreds of thousands of manufacturing jobs remain unfilled due to a lack of qualified applicants. This shortage disproportionately impacts sectors like advanced materials, precision manufacturing, and aerospace.
Addressing the Skills Gap through Education and Training
Bridging the skills gap requires a concerted effort to improve education and training programs. Government initiatives, private-sector partnerships, and community colleges all play a vital role in developing the skilled workforce needed for restored manufacturing jobs.
-
Examples of Successful Workforce Training Programs:
- Apprenticeships partnering with manufacturing companies
- Vocational schools focusing on advanced manufacturing technologies
- Online courses and certifications providing accessible training
- Community college programs offering associate degrees in manufacturing-related fields
- Industry-sponsored training programs focused on specific technologies
-
Funding Models and Effectiveness: Effective funding models must be explored to ensure the sustainability and accessibility of these programs. Public-private partnerships, government grants, and industry investment all contribute to funding these initiatives. The effectiveness of these programs needs continuous evaluation and improvement to meet the evolving needs of the manufacturing sector.
Attracting and Retaining a Manufacturing Workforce
Even with skilled workers, the manufacturing sector faces competition from other industries for talent. Attracting and retaining a qualified workforce requires a strategic approach focused on compensation, benefits, and improving the overall perception of manufacturing careers.
Competitive Wages and Benefits
Offering competitive salaries and comprehensive benefits packages is crucial for attracting and retaining skilled manufacturing workforce members. These benefits must be competitive with other high-skill sectors.
-
Comparison of Manufacturing Wages: While wages in manufacturing are increasing, they still need to be more competitive with some technology and engineering sectors to attract top talent. Data from the Bureau of Labor Statistics can be used to track wage trends and identify areas for improvement.
-
Impact of Benefits Packages: Comprehensive benefits—including health insurance, retirement plans, paid time off, and opportunities for professional development—are essential for worker retention and job satisfaction.
Improving the Image of Manufacturing Careers
Outdated perceptions of manufacturing jobs as dirty, dangerous, and low-paying deter many young people from pursuing careers in the field. Modern manufacturing is high-tech and innovative, requiring skilled problem-solvers and technologically adept individuals.
-
Strategies for Improving the Image:
- Outreach programs to high schools and community colleges
- Targeted media campaigns showcasing the modern realities of manufacturing
- Mentorship programs connecting experienced professionals with younger workers
- Highlighting the potential for career advancement and high earning potential
-
Showcasing Career Advancement: Emphasizing the opportunities for career growth, specialization, and leadership roles within the sector can attract ambitious individuals seeking long-term careers.
The Role of Automation and Technological Advancements
Automation and technological advancements are transforming the manufacturing landscape, creating both challenges and opportunities for the workforce.
Automation's Impact on Employment
Automation displaces some lower-skilled positions, but it also creates new, higher-skilled jobs requiring specialized training. Managing this transition effectively is crucial.
-
Jobs Most Susceptible to Automation: Repetitive, manual tasks are most vulnerable to automation. However, this automation creates the need for workers to maintain, program, and troubleshoot these automated systems.
-
Retraining Displaced Workers: Successful strategies for retraining displaced workers involve partnerships between government agencies, training institutions, and manufacturing companies to equip workers with in-demand skills.
The Need for Adaptable Workers
The rapid pace of technological change demands a workforce capable of continuous learning and adaptation. Lifelong learning and reskilling initiatives are essential for success in the modern manufacturing environment.
-
Importance of Continuous Learning: Employees must constantly upskill and reskill to adapt to new technologies and processes. This requires access to ongoing training opportunities and a culture that supports professional development.
-
Examples of Successful Reskilling Programs: Government-sponsored programs, industry-led initiatives, and employer-provided training all play a crucial role in facilitating reskilling and ensuring a workforce ready for the evolving demands of restored manufacturing jobs.
Conclusion
The ability of America to fill the restored manufacturing jobs hinges on effectively addressing the skills gap, attracting and retaining a skilled workforce, and adapting to the impact of automation. This requires a multi-pronged approach involving government, industry, and educational institutions working together. Investing in comprehensive workforce development programs, promoting the modern image of manufacturing, and providing opportunities for lifelong learning are crucial for ensuring the continued success of the revitalized American manufacturing sector. Let's work together to bridge the skills gap and secure a thriving future for restored manufacturing jobs and the American manufacturing jobs market as a whole.
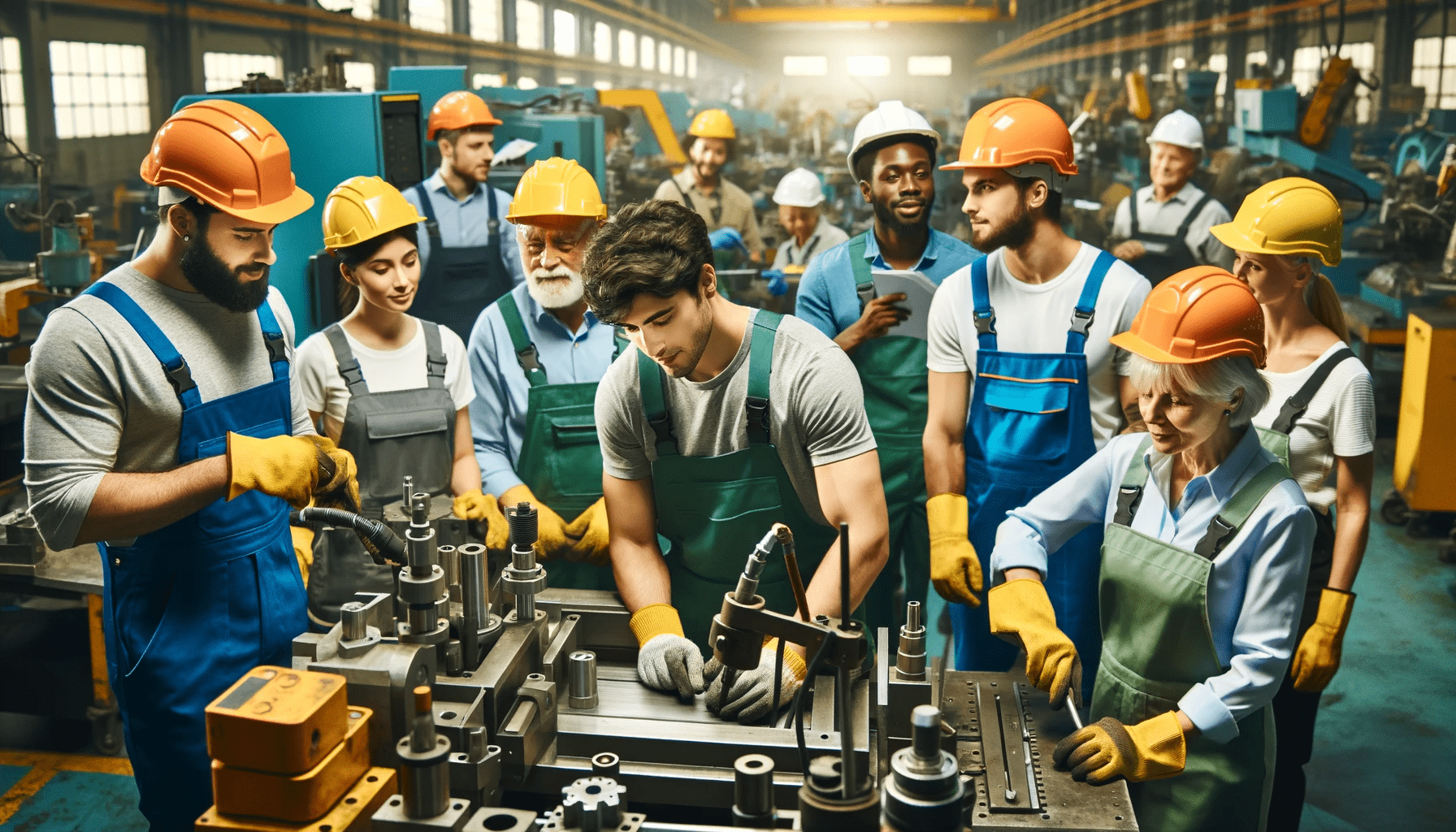
Featured Posts
-
Recent D Wave Quantum Qbts Stock Market Activity A Detailed Look
May 21, 2025 -
Exploring The World Of A Billionaire Boy From Inheritance To Innovation
May 21, 2025 -
D Wave Quantum Qbts Stocks Monday Plunge A Detailed Analysis
May 21, 2025 -
Breaking Wwe News Ronda Rousey Logan Paul Jey Uso And Big Es Engagement Rumors
May 21, 2025 -
Wwe Raw Tyler Bate And Pete Dunne Reunite
May 21, 2025