Challenges And Advancements In Automated Visual Inspection Systems For Lyophilized Vials
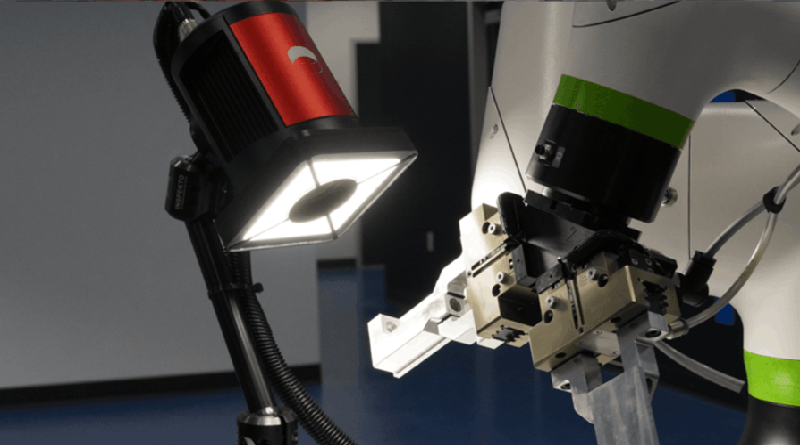
Table of Contents
Challenges in Automated Visual Inspection of Lyophilized Vials
Automated visual inspection of lyophilized vials is far from a simple task. Several significant challenges must be overcome to achieve reliable and high-throughput inspection.
Complex Defect Detection
Identifying defects in lyophilized vials is inherently difficult. The freeze-drying process creates a complex, often visually heterogeneous, lyophilized cake within the vial. This presents numerous challenges for automated systems:
- Variations in cake appearance: The appearance of the lyophilized cake can vary significantly depending on the formulation, the lyophilization process, and even the vial itself. This makes it difficult to establish consistent criteria for defect detection.
- Subtle crack detection: Identifying hairline cracks or other subtle defects in the cake requires extremely high resolution and sophisticated image processing techniques. These defects, while seemingly minor, can compromise product integrity.
- Impact of lighting and shadowing: The three-dimensional nature of the lyophilized cake and the vial geometry can create significant shadowing effects that obscure defects or create false positives.
- Challenges with high-throughput inspection: Meeting the demands of high-volume pharmaceutical production requires extremely fast inspection speeds without sacrificing accuracy. This presents a significant engineering challenge.
Differentiating between acceptable variations in cake appearance and actual defects is a major hurdle. The impact of different lyophilization cycles and formulations further complicates this process, necessitating highly adaptable and intelligent inspection systems.
High Throughput Requirements
Pharmaceutical manufacturing operates on a massive scale. Manual inspection simply cannot keep pace with the demands of modern production lines. Automated systems must achieve high throughput while maintaining exceptional accuracy:
- Balancing speed and accuracy: The speed of inspection needs to be optimized without compromising the ability to detect even subtle defects. This requires sophisticated algorithms and robust hardware.
- Impact on system cost: High-speed, high-accuracy inspection systems typically demand significant capital investment. The cost-effectiveness of automation must be carefully weighed against the potential benefits.
- Requirements for robust and reliable hardware: The automated system must be built to withstand the rigors of continuous operation in a demanding manufacturing environment. Reliability and minimal downtime are critical.
The economic benefits of automating visual inspection are undeniable. Switching from manual to automated systems dramatically reduces labor costs and improves overall efficiency, leading to significant cost savings in the long run.
Data Management and Analysis
Automated visual inspection generates enormous amounts of data. Effectively managing and analyzing this data is crucial for maintaining quality control and regulatory compliance:
- Data storage: The sheer volume of images and inspection results requires robust data storage solutions.
- Data processing: Efficient algorithms are essential for processing the data rapidly and extracting meaningful information.
- Statistical Process Control (SPC) integration: Integrating the automated inspection data with existing SPC systems provides a holistic view of the manufacturing process and enables proactive quality management.
- Regulatory compliance: Meeting stringent regulatory requirements necessitates careful documentation and traceability of all inspection data.
Sophisticated software and algorithms are critical for managing the data deluge generated by these systems. This includes efficient data storage, rapid processing, and seamless integration with existing quality control systems to ensure complete regulatory compliance.
Advancements in Automated Visual Inspection Technologies for Lyophilized Vials
Significant advancements in several areas are driving the improvement and wider adoption of automated visual inspection systems for lyophilized vials.
Advanced Image Processing Techniques
The application of advanced algorithms and machine learning is revolutionizing defect detection:
- Deep learning: Deep learning models can be trained to identify subtle defects that are difficult for traditional methods to detect.
- Computer vision: Computer vision techniques allow the system to "see" and interpret the images in a way that mimics human vision.
- Image segmentation: This technique helps to isolate the lyophilized cake from the vial background, improving defect detection accuracy.
- Pattern recognition: Identifying recurring patterns in acceptable and defective vials enhances the system's ability to distinguish between them.
These advanced techniques address many of the challenges associated with complex defect detection, significantly improving the accuracy and reliability of automated inspection systems.
Improved Hardware and Illumination Systems
Significant improvements in hardware and lighting are crucial for capturing high-quality images:
- High-resolution cameras: Higher resolution cameras provide significantly more detail, enabling the detection of even the smallest defects.
- Specialized lighting techniques: Techniques like structured light and polarized light can enhance image contrast and highlight subtle defects that might be otherwise invisible.
- Improved image acquisition speed: Faster cameras and image processing enable high-throughput inspection without sacrificing accuracy.
These hardware and illumination advancements contribute to superior image quality, leading to more reliable and accurate defect detection.
Integration with Existing Production Lines
Seamless integration with existing pharmaceutical manufacturing processes is critical for successful implementation:
- Automation integration: The automated system must integrate smoothly with the existing conveyor systems and other automation components on the production line.
- Data exchange protocols: Standard data exchange protocols ensure seamless communication between the inspection system and other systems in the manufacturing environment.
- Operator interface considerations: A user-friendly interface is essential for efficient operation and maintenance of the system.
- Validation and qualification: Rigorous validation and qualification processes are necessary to ensure that the system meets all regulatory requirements.
The challenges of retrofitting automated inspection systems into existing lines are significant. However, designing automation into new production lines from the outset offers substantial benefits in terms of efficiency and cost-effectiveness.
Conclusion
Automated visual inspection systems are essential for ensuring the quality and safety of lyophilized vials. While challenges remain, advancements in image processing techniques, hardware, and integration capabilities are paving the way for more accurate, efficient, and cost-effective solutions. The benefits include increased throughput, reduced labor costs, improved accuracy, and enhanced regulatory compliance. Improve your lyophilized vial quality control with advanced automated visual inspection solutions. Contact us today!
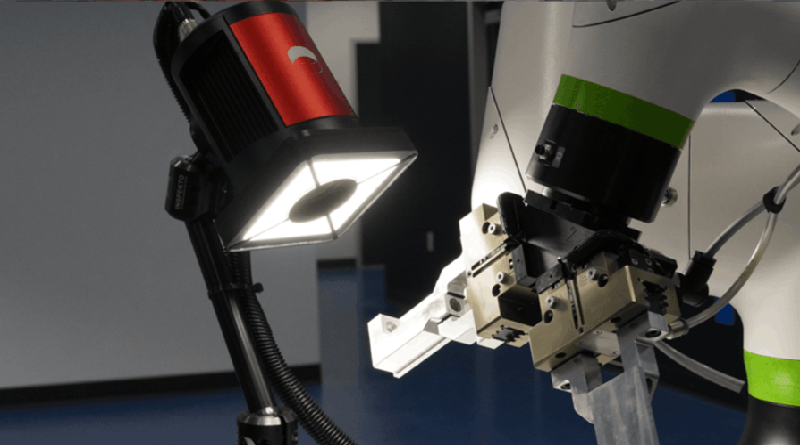
Featured Posts
-
Boris Dzonson Zrtva Napada Noja U Teksasu
May 11, 2025 -
Converse Signs Celtics Guard Payton Pritchard
May 11, 2025 -
Offshore Drilling In Uruguay The Search For Black Gold And Its Implications
May 11, 2025 -
Muellers Last Home Game Bayern Munichs Bundesliga Celebration
May 11, 2025 -
Prince Andrews Temper Explosive Outbursts Detailed By Former Royal Staff
May 11, 2025