Improving Productivity: A Key Issue For Carney's Leadership (Dodge)
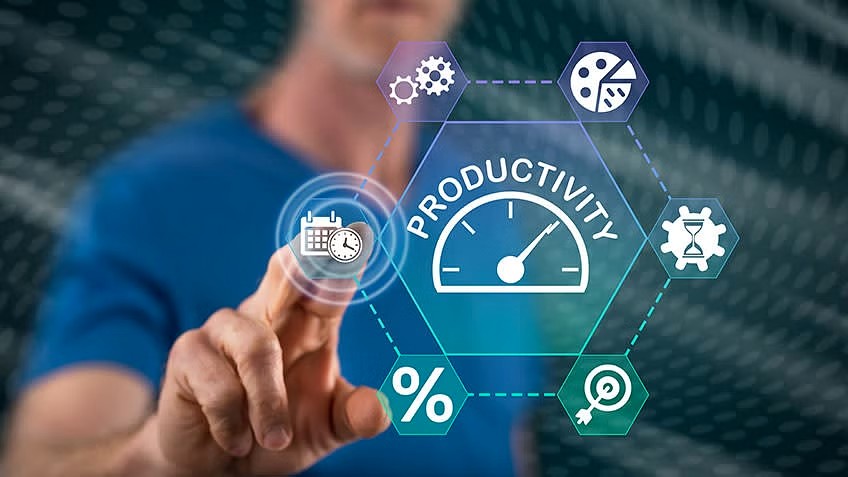
Table of Contents
Identifying the Root Causes of Declining Productivity at Dodge
Several interconnected factors contribute to the declining productivity at Dodge. Understanding these root causes is the first step towards implementing effective solutions. Key areas of concern include:
-
Low Morale and Employee Dissatisfaction: A decline in employee morale often manifests as decreased output and engagement. Factors such as lack of recognition, insufficient compensation, and stressful working conditions can significantly impact productivity. Addressing this requires a comprehensive review of employee satisfaction levels through surveys and feedback sessions.
-
Outdated Technology and Infrastructure: Reliance on outdated technology and inadequate infrastructure creates bottlenecks in workflows. Slow computers, inefficient software, and poor internet connectivity directly impact the speed and efficiency of tasks, hindering overall productivity. Investing in modern technology is crucial for improvement.
-
Inefficient Processes and Lack of Standardization: Inefficient processes and a lack of standardization across departments lead to wasted time, duplicated efforts, and increased error rates. This often stems from a lack of clearly defined workflows and procedures. Implementing lean methodologies and process mapping can address this challenge.
-
Inadequate Training and Skill Gaps: A lack of adequate training programs results in skill gaps among employees, hindering their ability to perform their tasks effectively. This lack of training can lead to increased errors, reduced efficiency, and a need for excessive supervision. Targeted training programs tailored to address specific skill gaps are essential.
-
Poor Communication and Collaboration: A breakdown in communication and collaboration between teams and departments slows down workflows and creates confusion. Lack of transparency, ineffective communication channels, and poor information sharing contribute significantly to reduced productivity.
-
Lack of Clear Goals and Performance Metrics: Without clearly defined goals and performance metrics, employees may lack direction and motivation. This absence of clear targets and measurable outcomes makes it difficult to track progress and identify areas for improvement. Establishing Key Performance Indicators (KPIs) is crucial.
Implementing Strategies to Enhance Employee Productivity at Dodge
Improving productivity at Dodge requires a multi-pronged approach focused on addressing the root causes identified above. Key strategies include:
-
Boosting Employee Engagement: Investing in employee engagement initiatives is crucial. This includes implementing employee recognition programs, fostering a positive work environment, promoting work-life balance, and providing opportunities for professional development. Happy and engaged employees are more productive.
-
Upgrading Technology and Infrastructure: Upgrading outdated technology and infrastructure is essential for improved workflow efficiency. This includes investing in new software, upgrading hardware, improving internet connectivity, and implementing cloud-based solutions to enhance collaboration and data accessibility.
-
Optimizing Processes and Workflows: Streamlining processes through process optimization techniques like Lean methodologies and Six Sigma can eliminate bottlenecks and redundancies. This involves mapping current workflows, identifying areas for improvement, and implementing standardized procedures to ensure efficiency.
-
Enhancing Employee Skills Through Training: Developing and implementing comprehensive training programs tailored to address specific skill gaps is crucial. This can involve on-the-job training, workshops, online courses, and mentorship programs to enhance employee skills and knowledge.
-
Improving Communication and Collaboration: Improving communication and collaboration can be achieved through regular team meetings, the use of collaborative software, transparent communication channels, and team-building activities. Fostering a culture of open communication and collaboration is key.
-
Implementing Robust Performance Management: Implementing a robust performance management system with clear goals, regular feedback, and performance reviews helps to ensure that employees are on track and that their performance is consistently evaluated. This enables timely identification of any performance issues and allows for appropriate corrective actions.
Measuring and Tracking Productivity Improvements at Dodge Under Carney's Leadership
Measuring and tracking progress is vital to ensure the effectiveness of implemented strategies. This requires a data-driven approach:
-
Establishing Key Performance Indicators (KPIs): Defining clear KPIs, such as output per employee, project completion rates, and customer satisfaction scores, is essential for tracking progress towards productivity goals.
-
Implementing Data Analysis: Regularly collecting and analyzing data on various productivity metrics allows for the identification of trends, bottlenecks, and areas requiring further improvement. This data should inform future decision-making.
-
Utilizing Data Visualization Tools: Using data visualization tools makes it easier to communicate progress to stakeholders, identify areas needing attention, and showcase the impact of implemented strategies. Clear visual representations are essential.
-
Developing a Reporting System: Establishing a system for regularly reporting on productivity improvements to Carney and other relevant leadership ensures transparency and accountability. This demonstrates the progress being made and helps to maintain momentum.
Conclusion
Improving productivity at Dodge under Carney's leadership requires a holistic approach that addresses both technological and human factors. By implementing the strategies outlined above— focusing on employee engagement, technology upgrades, process optimization, and improved communication—Dodge can achieve significant improvements in efficiency and overall productivity. Regular monitoring and data analysis are crucial for measuring the success of these initiatives and ensuring sustainable productivity gains. Addressing the challenge of improving productivity is vital for Carney's success at Dodge. By proactively implementing these strategies and consistently tracking progress, Dodge can overcome these hurdles and achieve sustainable productivity gains. Let's work together to improve productivity at Dodge!
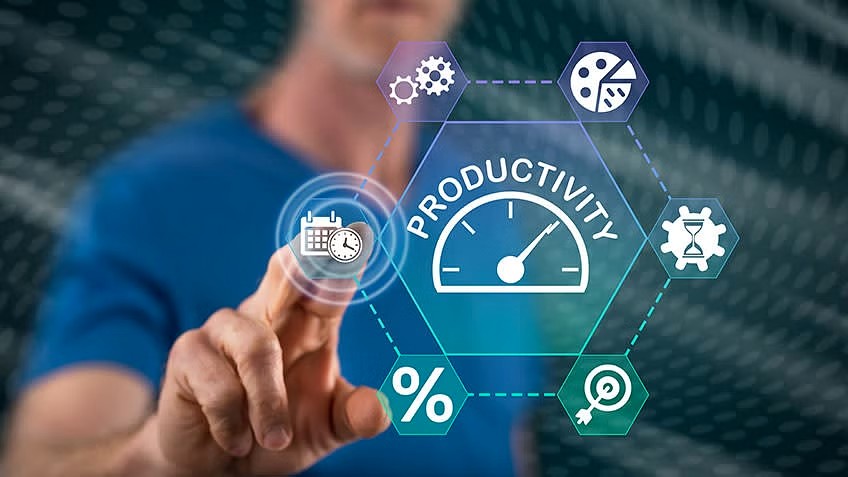
Featured Posts
-
Open Ai Under Ftc Scrutiny Chat Gpts Future In Question
May 08, 2025 -
Deandre Dzordan I Nikola Jokic Objasnjenje Njihovog Neobicnog Obicaja Ljubljenja
May 08, 2025 -
Bitcoins Current Rebound A Comprehensive Market Overview
May 08, 2025 -
Anons Pivfinaliv Ligi Chempioniv 2024 2025 Arsenal Proti Ps Zh Barselona Proti Intera
May 08, 2025 -
Mark Hamills New Role First Trailer For Stephen Kings The Long Walk
May 08, 2025
Latest Posts
-
Dwp Update Important Information Regarding Your Bank Account And 12 Benefits
May 08, 2025 -
Dwp Issues Warning Secure Your 12 Benefits Bank Account Action Needed
May 08, 2025 -
Why Scholar Rock Stock Dropped On Monday A Detailed Analysis
May 08, 2025 -
12 Dwp Benefits At Risk Verify Your Bank Details Now
May 08, 2025 -
Action Needed Dwps Four Word Warning Letter And Uk Benefit Changes
May 08, 2025