Improving The Accuracy Of Automated Visual Inspection For Lyophilized Vials
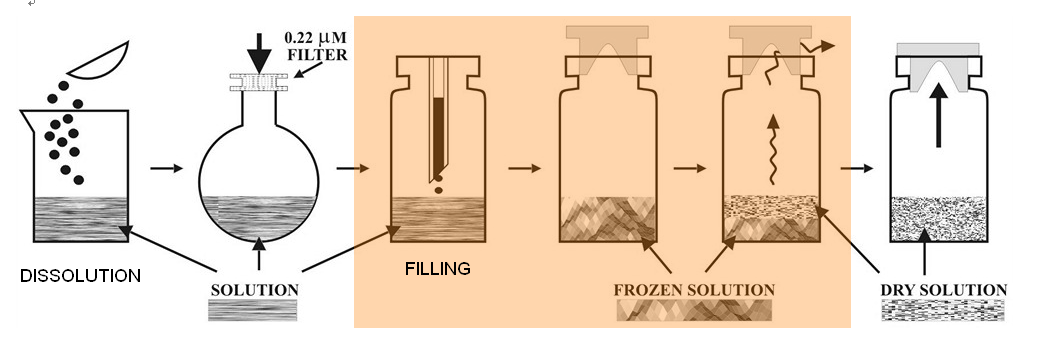
Table of Contents
Enhancing Image Acquisition for Improved Accuracy
High-quality images are the foundation of accurate automated visual inspection. Optimizing image acquisition significantly impacts the performance of AVI systems, particularly when dealing with the intricacies of lyophilized vials. Several factors contribute to optimal image capture:
-
Optimizing Lighting Conditions: Careful control of lighting is paramount. Shadows and reflections can obscure defects, leading to missed flaws. Exploring various lighting techniques, such as diffuse lighting (which minimizes shadows) and coaxial lighting (which reduces reflections), is critical. The choice depends on the vial's characteristics and the types of defects being targeted. Careful experimentation and analysis are needed to determine the ideal lighting setup for optimal defect detection.
-
High-Resolution Imaging: Employing high-resolution cameras equipped with appropriate lenses ensures that fine details are captured. The resolution should be sufficient to detect even the smallest cracks or inconsistencies in the lyophilized cake. However, increasing resolution necessitates consideration of processing speed; higher resolution images require more processing power and can slow down the inspection process. Finding the right balance is crucial for efficient and accurate AVI.
-
Depth of Field Control: Achieving consistent focus across the entire vial surface is vital, especially with variations in vial curvature. Controlling the depth of field through appropriate lens selection and focusing techniques helps maintain sharp images even across uneven surfaces. This minimizes blurry areas that could hinder defect detection.
-
Image Preprocessing: Before analysis, implementing image preprocessing techniques significantly improves accuracy. Noise reduction algorithms eliminate spurious signals that might be mistaken for defects. Sharpening algorithms enhance edges and details, making it easier for the algorithms to identify subtle imperfections. These preprocessing steps are essential for refining image quality and enhancing the system's sensitivity to defects.
Advanced Image Processing and Algorithm Development
Sophisticated algorithms are critical for interpreting the captured images and identifying defects. The application of advanced computer vision techniques, machine learning, and deep learning is transforming the field of automated visual inspection.
-
Computer Vision Algorithms: Implementing advanced computer vision algorithms such as edge detection, pattern recognition, and object classification enables the system to automatically identify and classify various defects. Convolutional Neural Networks (CNNs), a type of deep learning architecture, are particularly well-suited for image analysis tasks and are increasingly used in AVI systems for their superior performance in recognizing complex patterns.
-
Machine Learning and Deep Learning: Training machine learning and deep learning models on extensive datasets of images with known defects is essential for high accuracy. These models learn to identify subtle variations and patterns indicative of defects, improving their ability to detect even small imperfections that might be missed by traditional methods. The more diverse and representative the training data, the more robust and accurate the model becomes.
-
Algorithm Optimization: Continuously optimizing algorithms is crucial to minimize both false positives (incorrectly identifying a non-defect as a defect) and false negatives (missing actual defects). This process involves fine-tuning algorithm parameters, testing different algorithms, and incorporating feedback from real-world inspection data to continually improve performance and reliability.
-
Feedback Mechanisms: Integrating feedback mechanisms allows the system to learn from its mistakes and improve its accuracy over time. This could involve manual review of flagged images by human inspectors, providing corrective feedback that updates the algorithm's performance. This iterative approach is crucial for achieving high accuracy in real-world applications.
Addressing Challenges Specific to Lyophilized Vials
Lyophilized vials present unique challenges due to the nature of the lyophilization process. The appearance of the lyophilized cake can vary, making defect detection more complex.
-
Lyophilization-Specific Defects: Algorithms must be capable of specifically identifying defects common in lyophilized vials, including cracks, delamination (separation of layers), collapse (loss of vial integrity), and variations in cake appearance (e.g., unevenness, discoloration). The algorithms need to be trained to recognize the subtle visual cues associated with these defects.
-
Multi-spectral Imaging: Utilizing multi-spectral imaging can greatly enhance defect detection. This technique employs different wavelengths of light to reveal subtle variations in the lyophilized cake that might be invisible under standard lighting conditions. It can highlight differences in material composition or density, improving the accuracy of defect identification.
-
Process Understanding: Incorporating knowledge of the lyophilization process itself into algorithm design can dramatically improve accuracy. Understanding how process parameters affect the final cake appearance allows for the development of algorithms that can better differentiate between normal variations and actual defects.
Calibration and Validation for Consistent Results
Maintaining the accuracy and reliability of the AVI system over time requires rigorous calibration and validation procedures.
-
System Calibration: Regular calibration procedures are essential to maintain the accuracy of the system's measurements. This might involve using calibrated reference standards or images to ensure that the system’s responses remain consistent. Regular calibration minimizes the risk of drift in the system’s performance.
-
Validation and Regulatory Compliance: Thorough validation against established standards and regulatory requirements (e.g., Good Manufacturing Practices, or GMP) is crucial to demonstrate the system's accuracy and reliability. This involves documenting the system's performance and ensuring it meets the required specifications for its intended use.
-
Performance Monitoring: Continuously monitoring the system's performance helps identify and address any potential issues that might compromise accuracy. This involves tracking key metrics such as false positives, false negatives, and overall accuracy rates to identify trends and potential areas for improvement.
Conclusion
Improving the accuracy of automated visual inspection for lyophilized vials is critical for maintaining high pharmaceutical quality standards and patient safety. By optimizing image acquisition, utilizing advanced image processing and AI-powered algorithms, addressing the specific challenges of lyophilized products, and implementing robust calibration and validation procedures, manufacturers can significantly improve the efficiency and reliability of their quality control processes. Investing in advanced automated visual inspection systems and their ongoing optimization is paramount. Don't compromise on quality—improve the accuracy of your automated visual inspection for lyophilized vials today!
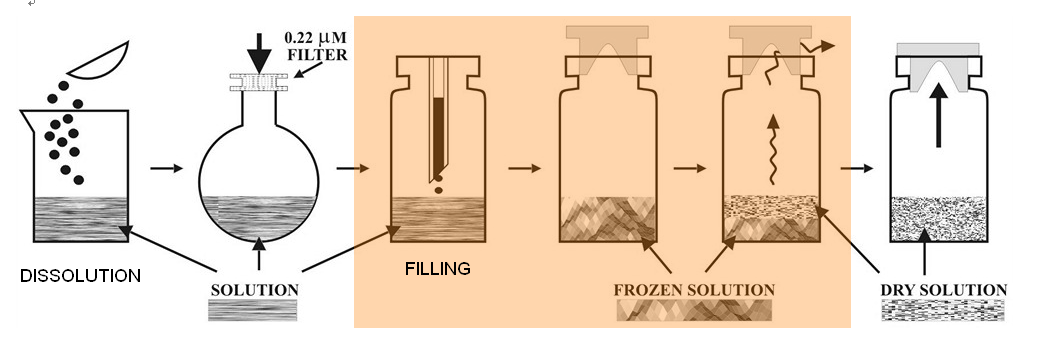
Featured Posts
-
Chainalysis Acquisition Of Alterya Boosting Blockchain Security With Ai
May 11, 2025 -
Bayern Munchen Ii Aduce Un Omagiu Lui Thomas Mueller
May 11, 2025 -
Meilleurs Placements Dans Quoi Investir Votre Argent Intelligemment
May 11, 2025 -
Foreign Airlines Acquire 25 Of West Jet Marking Onex Investment Exit
May 11, 2025 -
Choosing A College Town Why City Name Is A Top Contender
May 11, 2025