Robotic Challenges In Nike Sneaker Manufacturing: An In-Depth Look
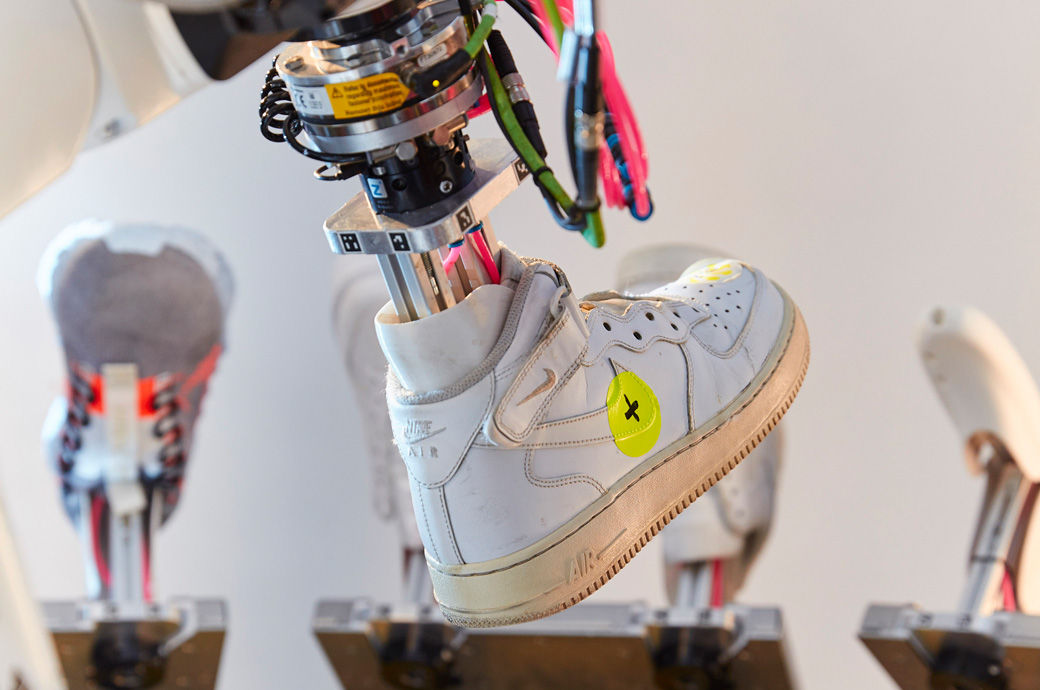
Table of Contents
Technological Hurdles in Robotic Sneaker Manufacturing
The intricate nature of sneaker assembly presents a significant technological barrier to complete automation. Robots, while powerful, still struggle with the dexterity and precision required for many tasks.
Dexterity and Precision
Current robotic arms lack the nuanced dexterity of human hands, leading to inconsistencies and defects. Tasks like:
- Stitching: Requiring precise needle control and consistent tension.
- Gluing: Demanding accurate application to avoid excess adhesive and ensure a strong bond.
- Attaching delicate components: Such as eyelets, logos, and other small parts, require fine motor skills robots currently lack.
Advanced sensor technology, coupled with improved control algorithms, is crucial to bridge this gap. Force sensors, vision systems, and tactile feedback mechanisms are vital for achieving the necessary precision. The development of more sophisticated robotic end-effectors, mimicking the adaptability of the human hand, is also essential.
Material Handling
Sneakers are constructed from a diverse array of materials, each presenting unique handling challenges for robotic grippers.
- Leather: Variable thickness and texture require adaptive gripping mechanisms.
- Textiles: Can be easily damaged by excessive force or improper handling.
- Rubber and Foam: Varying in stiffness and compliance, demanding grippers capable of secure yet gentle manipulation.
Robots need adaptive grippers capable of handling various textures, shapes, and sizes without causing damage. Improved material identification systems, using computer vision and other sensing technologies, are needed to ensure that robots correctly identify and handle different materials. This requires advanced AI and machine learning algorithms for efficient sorting and feeding systems.
Adaptability and Programming
Nike's production lines frequently switch between models and designs. Robots must be easily reprogrammed to adapt to these changes, a challenge requiring flexible and user-friendly programming interfaces.
- Intuitive Programming: Simplified programming interfaces using visual tools and natural language processing will reduce programming complexity and time.
- AI-Powered Adaptation: Artificial intelligence (AI) and machine learning (ML) are crucial for enabling robots to automatically adjust to variations in materials, processes, and designs. This adaptive learning is key for handling unexpected situations and ensuring consistent performance.
- Modular Design: Modular robotic systems allow for easier reconfiguration and adaptation to different production lines and product designs.
Economic Considerations of Robotic Implementation in Nike Factories
The high cost of implementing robotics in sneaker manufacturing poses a significant economic barrier.
High Initial Investment
The cost of purchasing and installing advanced robotic systems, including integration with existing infrastructure, is substantial. A thorough return on investment (ROI) analysis is essential, factoring in:
- Robot purchase price: The cost of advanced robots with the required dexterity and precision is high.
- Integration costs: Integrating robots into existing production lines requires significant engineering and labor.
- Maintenance and programming: Ongoing maintenance, repairs, and software updates add to operational expenses.
Government subsidies and tax incentives can help offset these high initial costs, encouraging wider adoption of automation technology.
Maintenance and Repair Costs
Sophisticated robotic systems require specialized expertise for maintenance and repair, leading to substantial ongoing expenses.
- Predictive Maintenance: Utilizing sensor data and AI to predict potential failures and schedule maintenance proactively minimizes downtime and reduces repair costs.
- Specialized Technicians: Training skilled technicians to maintain and repair these advanced systems is crucial for efficient operations.
- Spare Parts: A reliable supply of spare parts is essential for minimizing downtime due to equipment failures.
Job Displacement Concerns
Automating tasks previously done by human workers raises legitimate concerns about job displacement. A phased implementation strategy, coupled with investment in worker retraining, is essential to address this issue.
- Gradual Integration: A phased rollout allows for a smoother transition and minimizes sudden job losses.
- Retraining Initiatives: Investing in programs that retrain displaced workers for new roles within the factory or other sectors is crucial.
- Upskilling the Workforce: Training existing workers to operate and maintain robotic systems creates new job opportunities.
Logistical Challenges and Supply Chain Integration
Integrating robotic systems into existing production lines and managing the complexities of the supply chain present further logistical challenges.
Integration with Existing Production Lines
Integrating robotic systems into existing factories can be disruptive and complex.
- Careful Planning: Thorough planning and coordination are necessary to minimize disruption during the integration process.
- Modular Robotics: Modular robotic systems offer greater flexibility and easier integration into existing infrastructure.
- Phased Implementation: Integrating robots in stages, starting with less complex tasks, allows for gradual adaptation and reduces disruption.
Supply Chain Reliability
The reliable supply of robotic components, spare parts, and maintenance services is crucial for uninterrupted operation.
- Diversified Sourcing: Diversifying suppliers reduces the risk of disruptions due to single-source dependencies.
- Strategic Partnerships: Strong partnerships with suppliers ensure timely delivery of crucial components and support services.
- Inventory Management: Real-time monitoring and inventory management systems optimize the supply of necessary parts.
Conclusion: Overcoming Robotic Challenges in Nike Sneaker Manufacturing
The challenges of implementing robotics in Nike sneaker manufacturing are multifaceted, involving technological limitations, economic considerations, and logistical hurdles. While a fully automated factory remains a long-term goal, progress in robotics, AI, and collaborative human-robot systems is crucial for boosting efficiency, quality, and sustainability. Addressing these challenges—through innovation in robotic dexterity, adaptive gripping, AI-powered programming, and responsible workforce adaptation strategies—will unlock the full potential of robotics and revolutionize the future of Nike sneaker manufacturing. Continued investment and research are key to overcoming these robotic challenges and realizing the potential of advanced automation in the footwear industry.
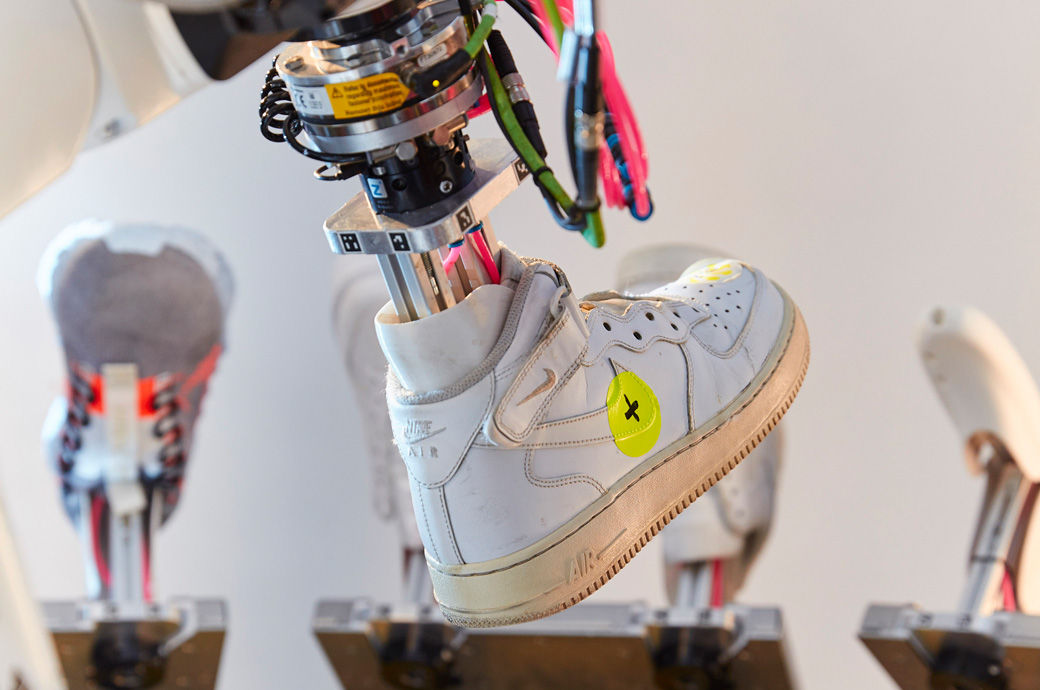
Featured Posts
-
Top Chinese Indonesian Officials Strengthen Security Cooperation
Apr 22, 2025 -
Anchor Brewing Company To Shutter A Legacy Ends
Apr 22, 2025 -
How Tik Tok Users Are Avoiding Trump Era Tariffs
Apr 22, 2025 -
Remembering Pope Francis A Champion Of Compassion And Social Justice
Apr 22, 2025 -
New Ev Technology Collaboration Saudi Aramco And Byd Join Forces
Apr 22, 2025