The Challenges Of Bringing Factory Jobs Back To The US
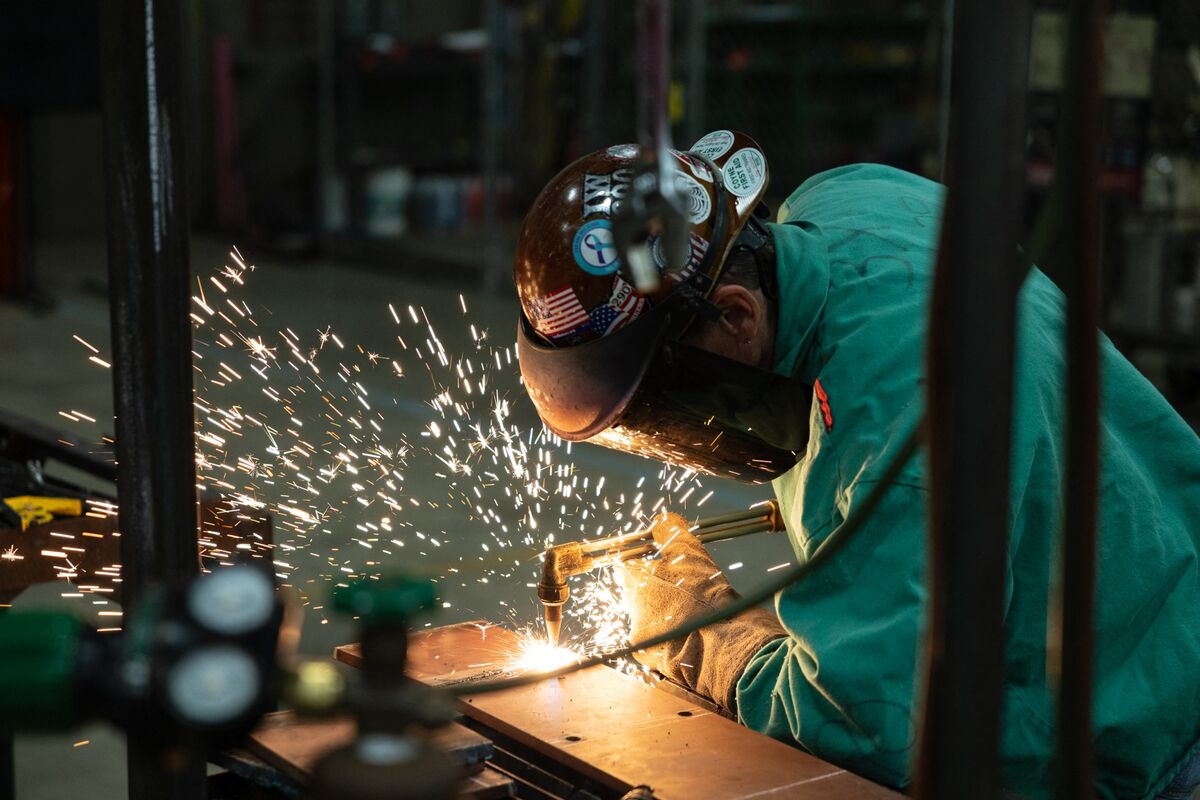
Table of Contents
High Labor Costs in the US Compared to Overseas Markets
One of the most significant barriers to reshoring is the considerable difference in labor costs between the US and many overseas manufacturing hubs. This disparity stems from several factors.
Minimum Wage and Benefits
The US boasts a significantly higher minimum wage and more comprehensive benefits packages compared to countries like China, Vietnam, or Mexico. This translates into higher overall labor costs for American manufacturers.
- Higher healthcare costs for employers: US healthcare costs are substantially higher than in many other countries, placing a considerable burden on employers.
- More stringent labor laws and regulations: The US has stricter labor laws and regulations, including requirements for paid time off, worker's compensation, and safety standards, all adding to the cost of employing workers.
- Unionization and associated increased labor costs: Unionization in the US often leads to higher wages and benefits, further increasing labor costs for companies.
- Comparison of average hourly wages across different countries: A simple comparison of average hourly manufacturing wages reveals a stark difference. For example, the average hourly wage in the US significantly exceeds that of its counterparts in Southeast Asia and even Mexico.
This significant cost difference makes it difficult for US-based manufacturers to compete with companies operating in lower-wage countries. The price competitiveness of goods manufactured in the US is directly impacted by this higher labor cost structure.
Automation and Technological Advancements Reducing the Need for Manual Labor
The rise of automation is another crucial factor impacting the feasibility of reshoring. Technological advancements are reducing the demand for manual labor in manufacturing, even as they increase overall efficiency and output.
Rise of Robotics and AI
Robotics and Artificial Intelligence (AI) are rapidly transforming the manufacturing landscape. Automated systems can perform tasks previously requiring human workers, often with greater speed, precision, and consistency.
- Increased efficiency and productivity through automation: Automation leads to significant gains in efficiency and productivity, allowing companies to produce more goods with fewer workers.
- Reduced labor costs through automation: While the initial investment in automation can be substantial, the long-term reduction in labor costs can be considerable.
- Examples of automated manufacturing processes: Automated assembly lines, robotic welding, and AI-powered quality control systems are just a few examples of how automation is reshaping manufacturing.
- The challenge of retraining workers displaced by automation: The shift toward automation necessitates retraining and upskilling the workforce to adapt to the changing demands of the industry. This presents a significant challenge, requiring investment in education and training programs.
While automation can enhance productivity and lower some costs, it also raises concerns about job displacement and the need for workforce adaptation, adding another layer of complexity to the reshoring equation.
Infrastructure Deficiencies and Logistics Challenges
The state of US infrastructure presents a significant hurdle to efficient manufacturing and transportation, impacting the overall cost-effectiveness of reshoring.
Aging Infrastructure and Transportation Costs
Aging infrastructure, including roads, railways, and ports, contributes to higher transportation costs and delays.
- Outdated transportation networks impacting timely delivery: Inefficient transportation networks lead to delays and increased costs for delivering goods to market.
- High transportation costs compared to other countries: The cost of moving goods within the US can be significantly higher compared to countries with more modern and efficient infrastructure.
- Lack of investment in modern infrastructure: A lack of significant investment in upgrading and modernizing US infrastructure contributes to these inefficiencies.
- The need for improved port facilities and inland waterways: Improved port facilities and inland waterways are essential for efficient handling of goods and reducing transportation bottlenecks.
Addressing these infrastructural deficiencies is vital for making US manufacturing more competitive and facilitating successful reshoring efforts.
Supply Chain Disruptions and Geopolitical Risks
Global supply chains are complex and vulnerable to disruptions, highlighting the risks associated with relying on foreign suppliers.
Global Supply Chain Complexity and Vulnerability
The intricate nature of global supply chains makes them susceptible to various risks.
- The impact of geopolitical instability on supply chains: Geopolitical events, such as trade wars or political instability, can severely disrupt supply chains, leading to shortages and delays.
- The vulnerability of relying on single-source suppliers: Over-reliance on single suppliers increases vulnerability to disruptions from unforeseen events.
- Risks associated with trade wars and tariffs: Trade wars and tariffs can significantly increase the cost of imported goods and materials, impacting the competitiveness of US manufacturers.
- The cost and difficulty of establishing domestic supply chains: Building robust domestic supply chains requires significant investment and can be a complex and time-consuming undertaking.
The complexities and risks associated with global supply chains underscore the need for a more diversified and resilient domestic supply chain to support reshoring initiatives.
Conclusion
Reshoring factory jobs to the US faces significant challenges: high labor costs, automation reducing the need for manual labor, inadequate infrastructure, and vulnerabilities within global supply chains. These factors combine to create a complex environment that demands thoughtful consideration and comprehensive solutions. However, the strategic importance of revitalizing US manufacturing and creating domestic jobs remains undeniable. Further research into reshoring initiatives, US manufacturing revival strategies, and government support programs for domestic job creation is essential. The long-term economic health and security of the US depend on addressing these challenges and finding effective pathways to bring factory jobs back to America.
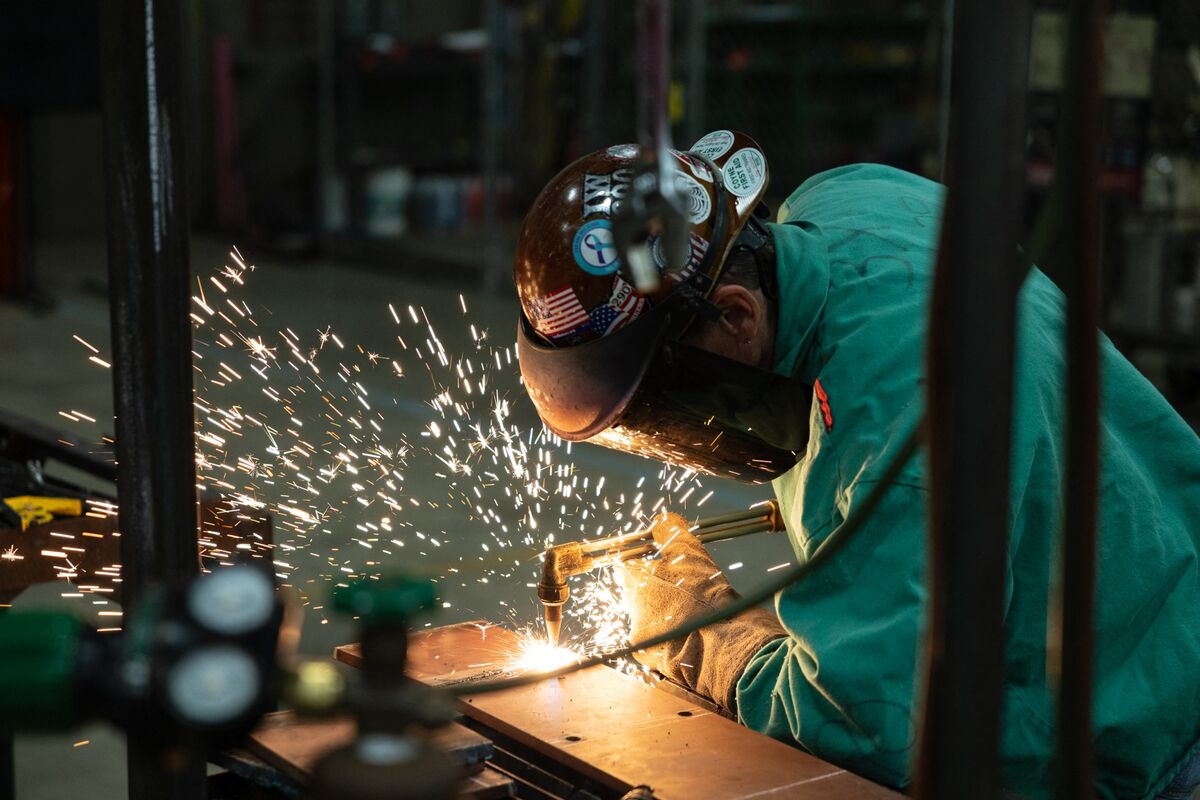
Featured Posts
-
Thursdays D Wave Quantum Qbts Stock Plunge What Happened
May 21, 2025 -
Possible Dexter New Blood Trailer Release Date Leak
May 21, 2025 -
Australian Foot Race Man Achieves Fastest Crossing
May 21, 2025 -
Irish Actor Barry Ward A Candid Interview On His Career
May 21, 2025 -
Sidirodromiko Diktyo Elladas Proodos I Stasis
May 21, 2025