The Fight For American Factory Jobs: Who Will Fill Them?
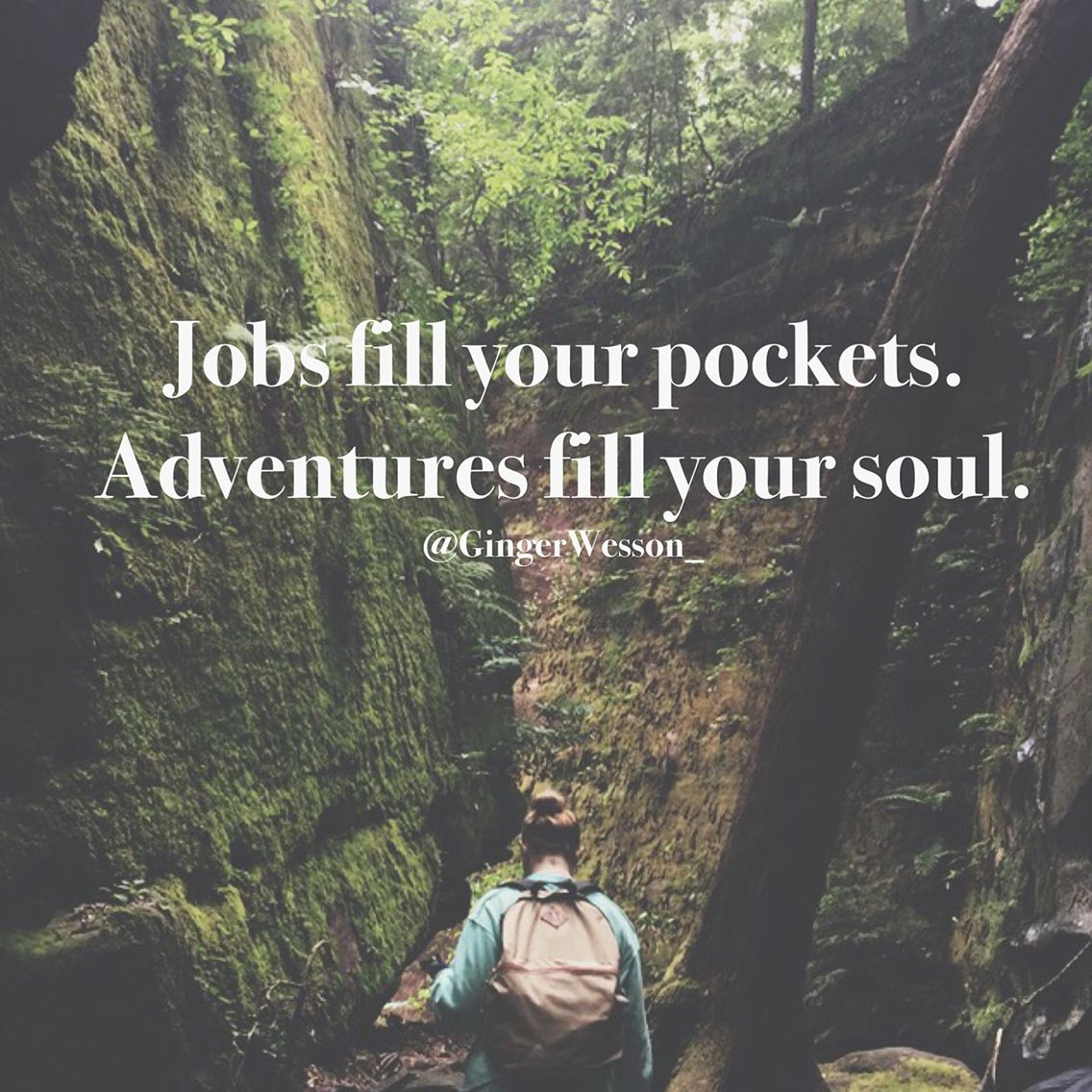
Table of Contents
The Skills Gap in American Manufacturing
The demand for skilled workers in American manufacturing significantly outpaces the supply, creating a substantial skills gap. This disparity threatens the ability of factories to meet production demands, hindering economic growth and competitiveness.
Demand for Skilled Workers Outpaces Supply
The modern manufacturing sector requires a highly skilled workforce proficient in a range of advanced technologies and techniques. The demand isn't just for basic assembly line workers; it's for individuals with specialized expertise.
- In-demand skills: Robotics operation and maintenance, PLC programming, CNC machining, advanced materials science, data analytics for manufacturing processes, and quality control using advanced technologies.
- Industries needing skilled workers: Automotive, aerospace, pharmaceuticals, electronics, and renewable energy sectors all face significant skilled labor shortages.
According to a recent report by the Manufacturing Institute, there are currently over 2 million unfilled manufacturing jobs in the United States. This staggering number highlights the urgent need for action to address the skills gap and ensure the future of American manufacturing jobs. [Source: Cite relevant report here].
The Impact of Automation on the Workforce
Automation is rapidly transforming the manufacturing landscape. While it's often perceived as a job killer, the reality is more nuanced. Automation eliminates some jobs, while simultaneously creating others that require new, highly specialized skills.
- Automation technologies impacting job roles: Robotics, AI-powered quality control systems, 3D printing, and advanced computer numerical control (CNC) machining are reshaping the manufacturing process.
- Changing nature of work: Automation requires workers to adapt, develop new skills, and focus on tasks requiring critical thinking, problem-solving, and complex system management. This necessitates a significant focus on reskilling and upskilling initiatives.
Addressing the Shortage: Education and Training Initiatives
Bridging the skills gap requires a multi-faceted approach involving significant investment in education and training programs. This involves empowering individuals with the skills needed for success in modern manufacturing settings.
The Role of Vocational Schools and Community Colleges
Vocational schools and community colleges play a vital role in providing targeted training for manufacturing jobs. Successful programs focus on strong industry partnerships to ensure curricula are aligned with current industry needs and offer hands-on experience.
- Examples of successful vocational training programs: Apprenticeships, industry-sponsored training programs, and partnerships between educational institutions and manufacturing companies.
- Job placement rates and starting salaries: Data shows that graduates of successful programs enjoy high job placement rates and competitive starting salaries, demonstrating the effectiveness of targeted training. [Source: Cite relevant data here].
Government Initiatives and Funding for Workforce Development
Government support is crucial for expanding access to quality manufacturing training programs. Federal and state initiatives provide funding for training and education programs, contributing to the development of a skilled workforce.
- Examples of government initiatives: Grants for vocational schools, tax credits for companies investing in employee training, and public-private partnerships to develop industry-specific training programs.
- Effectiveness and improvement suggestions: While government programs play a vital role, ongoing evaluation and adaptation are crucial to ensure their effectiveness and responsiveness to evolving industry needs. More funding and a streamlined process for accessing funds are needed to maximize impact.
Attracting and Retaining Workers: Beyond Skills
Attracting and retaining skilled workers requires more than just training; it involves creating a positive and rewarding work environment. Competitive compensation and a positive company culture are essential factors.
Competitive Wages and Benefits Packages
Offering competitive wages and benefits is paramount to attracting and retaining top talent in manufacturing. Compensation should reflect the skill level and responsibility of the roles.
- Attractive benefits packages: Health insurance, retirement plans, paid time off, paid parental leave, and opportunities for professional development.
- Positive work environment and company culture: A safe, respectful, and engaging work environment is crucial for employee satisfaction and retention.
Improving the Image of Manufacturing Careers
Manufacturing jobs are often unfairly perceived as low-skill and low-paying. Efforts must be made to change this outdated perception.
- Highlighting positive aspects: Emphasize the problem-solving, innovation, technology, and creativity inherent in modern manufacturing roles.
- Successful marketing campaigns: Public relations campaigns that showcase modern manufacturing environments and career advancement opportunities can attract young people to the field.
Conclusion
The fight for American factory jobs is a fight for the future of American manufacturing. Addressing the critical shortage of skilled workers requires a concerted effort involving investment in vocational training, government initiatives to support workforce development, competitive compensation and benefits packages, and a concerted effort to improve the image of manufacturing careers. The key takeaways are clear: a strategic approach to education and training, coupled with a commitment to creating attractive work environments, is essential. The future of American manufacturing depends on addressing this critical shortage of skilled workers. Learn more about available training programs and how you can contribute to the fight for American factory jobs today!
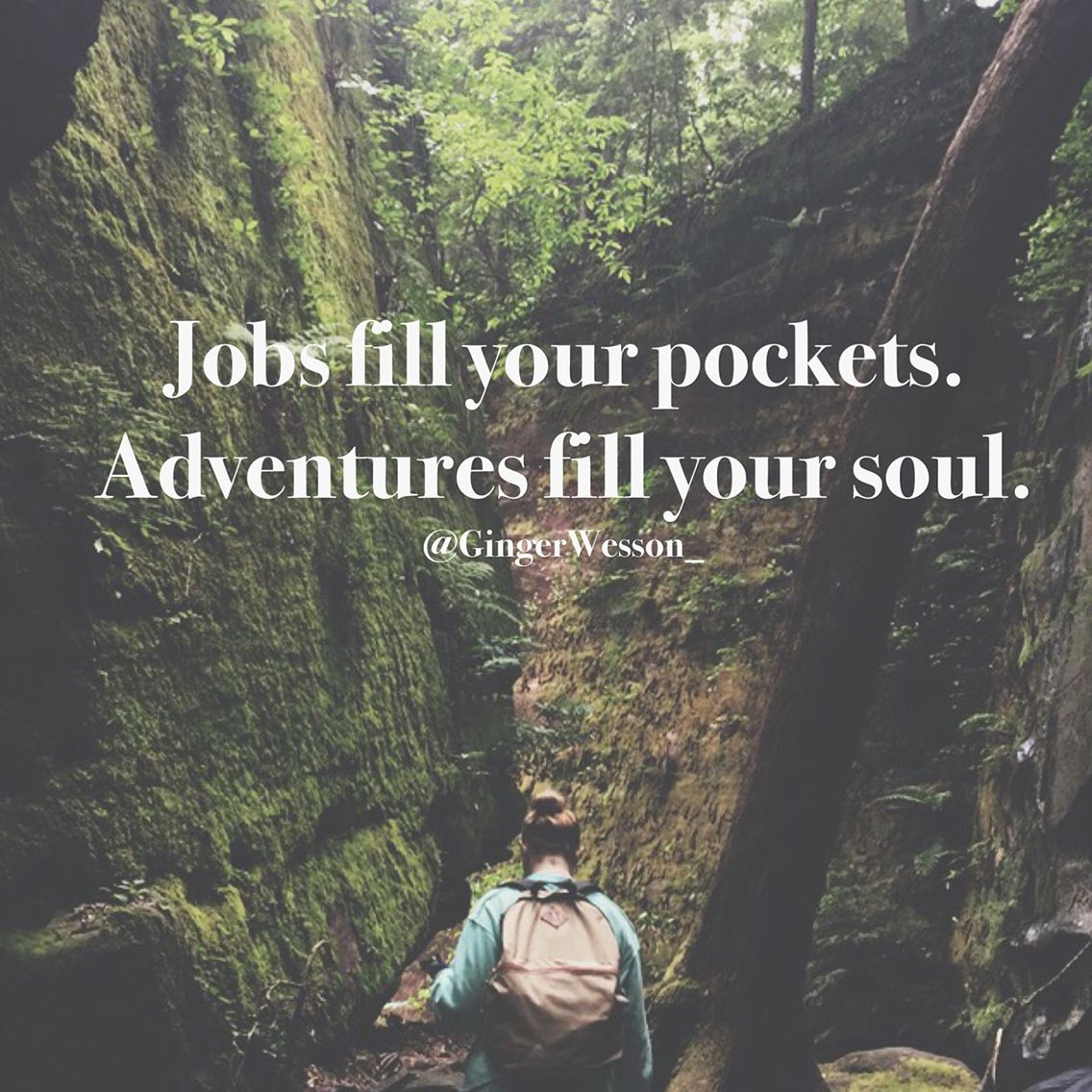
Featured Posts
-
Situatsiya S Shumakherom Ostaetsya Pechalnoy Novye Podrobnosti Ot Druga
May 20, 2025 -
Jennifer Lawrence And Cooke Maroney Expand Their Family
May 20, 2025 -
2024 Formula 1 Sezonu Takvim Sueruecueler Ve Daha Fazlasi Icin Geri Sayim
May 20, 2025 -
Nouveaux Restaurants A Biarritz Adresses Et Chefs A Decouvrir
May 20, 2025 -
Cote D Ivoire Le Salon International Du Livre D Abidjan Ouvre Ses Portes Pour Sa 15eme Edition
May 20, 2025