The High Cost Of Making An All-American Product
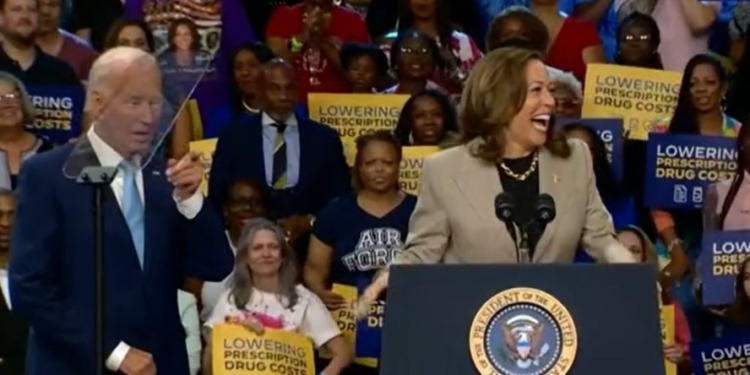
Table of Contents
Soaring Labor Costs in the US
One of the most significant factors driving up the cost of making an All-American product is the expense of labor. US workers command significantly higher wages and benefits than their counterparts in many other manufacturing hubs globally. This difference directly impacts the overall production cost.
Higher Wages and Benefits
- Higher Minimum Wage: The US minimum wage is substantially higher than in many countries, impacting even entry-level positions in manufacturing.
- Comprehensive Benefits Packages: American workers typically receive comprehensive benefits packages including health insurance, paid sick leave, retirement plans (401k), and paid vacation time. These benefits, while crucial for employee well-being, add considerably to labor costs. For example, employer-sponsored health insurance can add thousands of dollars per employee annually.
- Wage Comparison: The average hourly wage for manufacturing workers in the US is significantly higher than in countries like China, Vietnam, or Mexico. This disparity reflects not only base pay but also the inclusion of benefits. A recent study showed a 300% difference in average manufacturing wages between the US and certain Southeast Asian countries.
Skilled Labor Shortages
The US manufacturing sector also faces significant challenges in finding and retaining skilled workers. This shortage leads to increased recruitment and training costs, further driving up production expenses.
- Aging Workforce: Many skilled manufacturing workers are approaching retirement age, creating a gap in expertise.
- Lack of Interest in Manufacturing Careers: Manufacturing jobs are often perceived as less desirable than other career paths, leading to a smaller pool of qualified applicants.
- Strategies to Attract Talent: To compete for skilled workers, US manufacturers often need to offer higher salaries, enhanced benefits packages, and comprehensive training programs, adding to their overall operational costs.
Raw Material and Supply Chain Challenges
Sourcing raw materials and managing the supply chain represent another significant hurdle for American manufacturers. The cost of domestic sourcing often surpasses that of importing materials from countries with lower production costs.
Sourcing Domestic Materials
- Limited Domestic Supply: The US may not have a readily available domestic supply for all the raw materials needed for certain products. This necessitates sourcing from other countries, negating some of the benefits of domestic production.
- Higher Domestic Prices: Even when domestic sources exist, the price of raw materials is often higher in the US than in other parts of the world.
- Transportation Costs: Transporting raw materials across the vast US landscape adds to the overall cost. This is especially true for bulky or heavy materials.
Increased Transportation Costs
Transportation costs within the US contribute significantly to the price of All-American products.
- Fuel Price Volatility: Fluctuations in fuel prices directly impact transportation costs, making it challenging for manufacturers to accurately predict and manage their expenses.
- Logistical Complexities: The US's extensive transportation infrastructure, while robust, can present logistical challenges and delays, adding to the overall cost. Shipping goods across state lines, for instance, is often more expensive than international shipping to certain regions.
Regulatory Compliance and Environmental Regulations
The US has stringent environmental regulations and robust safety standards for manufacturing. While these regulations protect workers and the environment, they increase the cost of production.
Stringent Environmental Standards
- Emission Controls: Manufacturers must invest in expensive equipment and processes to meet strict emission standards, adding significant capital costs.
- Waste Management: Regulations surrounding waste disposal and recycling add to operational expenses.
- Certifications: Obtaining and maintaining environmental certifications adds another layer of cost.
Bureaucracy and Permits
Navigating the regulatory landscape in the US requires significant time and resources.
- Permitting Processes: Obtaining permits and licenses can be a time-consuming and costly process, often involving multiple agencies and levels of government.
- Compliance Audits: Regular compliance audits are necessary to ensure adherence to regulations, adding to administrative overhead.
- Legal Fees: Manufacturers might require legal counsel to navigate complex regulations, leading to additional expenses.
Tariffs and Trade Policies
Tariffs and trade policies significantly impact the cost of producing All-American products.
Impact of Tariffs on Imported Goods
- Increased Material Costs: Tariffs on imported raw materials or components increase the cost of manufacturing, making domestically produced goods less competitive.
- Retaliatory Tariffs: The imposition of tariffs can trigger retaliatory tariffs from other countries, further complicating the situation and raising costs.
Trade Agreements and their Influence
Negotiations and renegotiations of trade agreements can directly impact the cost of making an All-American product.
- Import Costs: Trade agreements can either lower or raise the cost of imported goods, affecting the competitiveness of domestic manufacturers.
- Market Access: Trade agreements influence the market access for US-made goods, impacting their price and overall competitiveness.
Conclusion
The high cost of making an All-American product is a result of a complex interplay of labor costs, supply chain complexities, stringent regulations, and the impact of tariffs and trade policies. While the "Made in USA" label holds significant appeal for consumers, it's crucial to understand the economic realities involved. These costs are often passed on to consumers, resulting in higher prices for domestically produced goods.
Are you willing to pay more for an All-American product, knowing the economic realities behind its production? Consider the factors discussed above when making purchasing decisions, and support American businesses that are transparent about the costs involved in creating truly All-American products. By understanding the challenges facing domestic manufacturers, you can make informed choices that support both American jobs and responsible consumption.
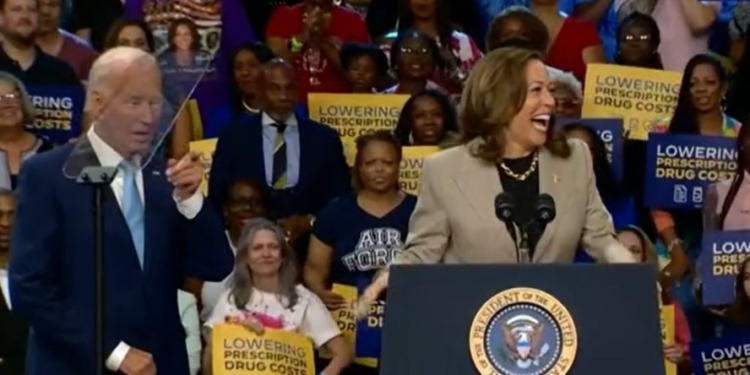
Featured Posts
-
Willie Nelson And Family An Austin City Limits Concert Retrospective
Apr 29, 2025 -
Cnn Reports Over 100 Immigrants Detained In Underground Nightclub Raid
Apr 29, 2025 -
Over 100 Immigrants Detained In Underground Nightclub Raid Cnn Video Evidence
Apr 29, 2025 -
Adidas Anthony Edwards 2 A First Look At The New Signature Shoe
Apr 29, 2025 -
Solve The Nyt Spelling Bee February 10 2025 Puzzle
Apr 29, 2025
Latest Posts
-
Trial Of The Century Cardinals Legal Team Presents Evidence Of Prosecutorial Misconduct
Apr 29, 2025 -
Cardinal Beccius Unfair Trial Claim Bolstered By New Evidence
Apr 29, 2025 -
Reviving Nostalgia Older Viewers And Their You Tube Habits
Apr 29, 2025 -
How You Tube Is Attracting A Growing Audience Of Older Viewers
Apr 29, 2025 -
London Real Estate Fraud British Court Upholds Vaticans Claim
Apr 29, 2025