Why Making An All-American Product Is So Difficult
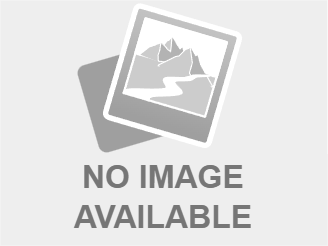
Table of Contents
The High Cost of Domestic Manufacturing
One of the most significant obstacles to creating an All-American product is the substantially higher cost of manufacturing domestically compared to overseas production. This cost differential stems from several key factors:
Labor Costs
American wages are significantly higher than in many other countries, a major driver of increased production expenses.
- Minimum wage variations across states: The minimum wage varies considerably from state to state, impacting labor costs even within the US.
- Benefits packages: American companies typically provide more comprehensive benefits packages, including health insurance and retirement plans, adding to overall labor expenses.
- Unionization impact: Unionized workplaces often command higher wages and benefits, further increasing labor costs.
Compared to countries like China or Mexico, average labor costs in the US are significantly higher, often impacting the price competitiveness of domestically produced goods. This difference can make it difficult for American manufacturers to compete with lower-priced imports.
Raw Material Sourcing
Securing all necessary raw materials domestically presents another considerable challenge. Many essential materials are either not readily available in the US or are significantly more expensive to source within the country.
- Reliance on imports for specific materials: American manufacturers often rely on imports for various raw materials, including certain metals, chemicals, and textiles.
- Transportation costs: Transporting raw materials across the country adds to the overall cost, especially for bulky or heavy materials.
- Supply chain vulnerabilities: Relying on domestic sources can reduce vulnerability to global supply chain disruptions but can also be more susceptible to regional issues impacting specific resources.
Industries like electronics manufacturing, which rely on rare earth minerals often sourced from China, exemplify the difficulties in achieving complete domestic sourcing. This dependence on foreign suppliers creates both economic and national security concerns. The quest for sustainability further complicates this, as sourcing eco-friendly materials domestically can prove even more challenging and costly.
Regulatory Compliance and Environmental Standards
The United States boasts stringent environmental regulations and safety standards, designed to protect both workers and the environment. While these regulations are crucial, they add a considerable layer of cost to the manufacturing process.
- Environmental Protection Agency (EPA) regulations: EPA regulations dictate stringent environmental controls, impacting everything from waste disposal to emissions.
- Safety standards: Occupational Safety and Health Administration (OSHA) standards mandate robust workplace safety measures, increasing compliance costs.
- Compliance costs: Navigating complex regulations requires specialized expertise and significant investment in compliance programs.
Meeting these standards necessitates investment in specialized equipment, rigorous testing procedures, and meticulous record-keeping, all contributing to higher manufacturing costs. While environmentally responsible practices are critical, the associated costs present another challenge to achieving cost-competitive All-American production.
Competition from Global Markets
The challenge of creating an All-American product extends beyond domestic costs; American manufacturers must also contend with intense competition from global markets.
Lower Production Costs Overseas
Foreign manufacturers often benefit from significantly lower labor and material costs, allowing them to undercut American prices.
- Global supply chains: Established global supply chains offer economies of scale and cost efficiencies that are often difficult to replicate domestically.
- Offshoring: Many companies choose to offshore production to take advantage of lower labor and production costs.
- Price wars: The intense global competition often leads to price wars, making it difficult for American manufacturers to maintain profitability.
Globalization has fundamentally reshaped the manufacturing landscape, creating intense competition for American businesses. Industries like apparel and textiles have seen a significant shift in production overseas, highlighting the impact of lower labor costs on global competitiveness.
Trade Policies and Tariffs
International trade agreements and tariffs significantly influence the competitiveness of domestically manufactured goods.
- Impact of tariffs on import prices: Tariffs increase the cost of imported goods, potentially making domestic products more competitive. However, they can also lead to retaliatory tariffs, harming American exports.
- Trade negotiations: The ongoing negotiations surrounding trade agreements heavily impact the playing field for American manufacturers.
- Free trade agreements: Free trade agreements aim to reduce barriers to trade but can also lead to increased competition from foreign producers.
The dynamic nature of international trade policies creates uncertainty and makes long-term strategic planning challenging for companies aiming to produce All-American products. Trade wars and retaliatory tariffs can dramatically impact the cost and availability of both imported goods and American exports.
Maintaining Skilled Labor and Technological Advancement
Producing high-quality All-American goods requires a skilled workforce and ongoing investment in advanced manufacturing technologies.
Skills Gap in Manufacturing
Finding and retaining skilled workers in the manufacturing sector is an ongoing challenge in the US.
- Lack of vocational training: A shortage of skilled labor is partly due to a decline in vocational training and apprenticeships.
- Attracting young talent: Manufacturing needs to compete with other industries to attract young, skilled workers.
- Employee retention strategies: Retaining experienced and skilled workers requires competitive compensation and benefits packages.
Addressing the skills gap requires a concerted effort to revitalize vocational training programs and make manufacturing careers more attractive to young people. Investment in education and apprenticeship programs is crucial for building a strong and skilled workforce.
Investing in Automation and Technology
Staying competitive in the global marketplace necessitates significant investment in advanced manufacturing technologies.
- Robotics: Implementing robotics and automation can increase efficiency and productivity.
- AI: Artificial intelligence is transforming manufacturing processes, improving quality control and optimizing production.
- Automation costs: The upfront cost of adopting automation technologies can be substantial.
- Return on investment: The return on investment from automation varies depending on the specific technology and industry.
The adoption of advanced manufacturing technologies like robotics and AI is crucial for improving efficiency, reducing labor costs, and enhancing product quality. However, the high initial investment required presents a considerable hurdle for many American manufacturers.
Conclusion
Making a truly All-American product presents considerable challenges, from high production costs and fierce global competition to the need for skilled labor and technological innovation. Overcoming these hurdles requires a multifaceted approach involving government support, industry collaboration, and a commitment to investing in both human capital and technological advancement. The pursuit of strengthening domestic manufacturing requires addressing these interconnected challenges.
While the path to creating an All-American product is undeniably difficult, the rewards – both economically and in terms of national pride – make the pursuit worthwhile. Learn more about strategies for successfully navigating the challenges of domestic manufacturing and discover how to increase your chances of creating your own successful All-American product. Investing in reshoring and creating a robust domestic manufacturing sector is key to building a stronger and more resilient American economy.
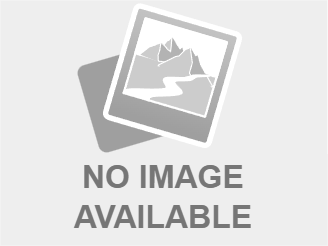
Featured Posts
-
Winners Of Minnesotas Snow Plow Naming Contest
Apr 29, 2025 -
Tylor Megills Success With The Mets Pitching Strategies And Results
Apr 29, 2025 -
La Garantia De Gol De Alberto Ardila Olivares Un Analisis
Apr 29, 2025 -
Khaznas Saudi Arabia Expansion A Post Silver Lake Investment Strategy
Apr 29, 2025 -
Abrz Mealm Fn Abwzby 2024 Bdayt Alerd 19 Nwfmbr
Apr 29, 2025
Latest Posts
-
You Tubes Growing Popularity Among Older Viewers A Resurgence Of Classic Shows
Apr 29, 2025 -
How Npr Explains You Tubes Expanding Older Adult User Base
Apr 29, 2025 -
Is You Tube Becoming A Senior Destination Npr Explores The Shift
Apr 29, 2025 -
The Rise Of Older You Tube Users Data And Insights From Npr
Apr 29, 2025 -
Analyzing You Tubes Growth Among Older Demographics An Npr Perspective
Apr 29, 2025