Automated Visual Inspection Of Lyophilized Vials: Challenges And Solutions
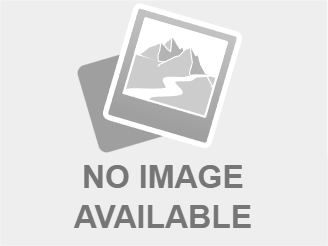
Table of Contents
Challenges in Automated Visual Inspection of Lyophilized Vials
Automating the visual inspection of lyophilized vials is complex due to several inherent difficulties. The freeze-drying process itself introduces variability, making consistent automated defect detection a significant challenge.
Variability in Lyophilized Product Appearance
The freeze-drying process, while crucial for preserving the efficacy of pharmaceuticals, can lead to inconsistencies in the final product's appearance. These variations complicate automated detection systems. Slight differences in the lyophilized cake's structure, the presence of cracks, or variations in color can be subtle yet critical indicators of compromised product quality. Automated systems must be sophisticated enough to discern these nuances from acceptable variations.
- Cracks: Fine cracks in the lyophilized cake can indicate instability or compromised product integrity.
- Collapse: Partial or complete collapse of the cake can affect drug stability and reconstitution.
- Particulate Matter: The presence of foreign particles within the vial is unacceptable and requires detection.
- Discoloration: Changes in color can signify degradation or contamination of the drug substance.
Lighting and Image Acquisition Challenges
Obtaining high-quality images of lyophilized vials for automated inspection is far from straightforward. The transparency of the glass vials, coupled with the often-translucent nature of the lyophilized product, creates significant challenges in image acquisition. Light reflection and shadowing can obscure critical details, hindering accurate defect detection.
- Brightfield Illumination: Provides overall vial and cake visibility but may struggle with subtle defects.
- Darkfield Illumination: Highlights surface imperfections but may lack sufficient detail for internal defects.
- Coaxial Illumination: Reduces reflections but might not be suitable for all vial types and product characteristics.
Data Analysis and Algorithm Development
Developing reliable algorithms to detect subtle defects in lyophilized vials is computationally intensive. The algorithms must be robust enough to handle the natural variations in product appearance while maintaining high sensitivity to critical defects. This requires sophisticated image processing techniques and advanced machine learning approaches.
- Machine Learning (ML): ML algorithms can learn from large datasets of images, improving their ability to identify defects.
- Deep Learning (DL): DL models, a subset of ML, offer higher accuracy through complex neural network architectures.
- Computer Vision: Computer vision techniques are crucial for image analysis, feature extraction, and defect classification.
Integration with Existing Production Lines
Integrating automated visual inspection systems into existing pharmaceutical manufacturing lines requires careful planning and consideration. Throughput, space constraints, and compatibility with other equipment are all critical factors. Cleaning validation and maintaining sterility are also paramount concerns.
- Speed and Throughput: The system must keep pace with existing production line speeds.
- Space Constraints: Integration must consider the available space within the manufacturing facility.
- Cleaning Validation: The system must be designed for easy cleaning and validation to meet regulatory requirements.
Solutions for Automated Visual Inspection of Lyophilized Vials
Addressing the challenges detailed above necessitates the adoption of advanced technologies and strategies. The following solutions are paving the way for more accurate and efficient automated visual inspection.
Advanced Imaging Techniques
Utilizing high-resolution cameras and specialized lighting techniques significantly improves the quality of images obtained. Advanced methods like multi-spectral imaging provide additional information beyond the visible spectrum, enhancing defect detection.
- Hyperspectral Imaging: Captures images across a wide range of wavelengths, revealing subtle variations in material composition.
- 3D Imaging: Provides three-dimensional views of the lyophilized cake, allowing for more comprehensive defect analysis.
Improved Algorithm Development
The application of machine learning and AI is revolutionizing automated defect detection. Training algorithms with large, diverse datasets improves their accuracy and robustness in handling variations in lyophilized product appearance. Continuous algorithm improvement through techniques such as data augmentation and transfer learning is crucial for maintaining optimal performance.
- Data Augmentation: Artificially increasing the size of the training dataset by creating modified versions of existing images.
- Transfer Learning: Leveraging pre-trained models to accelerate the training process and improve accuracy.
Robotic Integration and Automation
Robotic systems automate the handling and positioning of vials, ensuring consistent and efficient inspection. This not only increases throughput but also significantly reduces human error. Proper system integration is crucial to ensure seamless operation within the existing manufacturing process.
- Robotic Arms: Used for picking, placing, and orienting vials for inspection.
- Automated Guided Vehicles (AGVs): Transport vials between different stages of the manufacturing process.
Conclusion
Automated Visual Inspection of Lyophilized Vials presents significant challenges, primarily related to product variability, image acquisition, algorithm development, and system integration. However, advanced imaging techniques, improved algorithm development through machine learning and AI, and robotic automation are providing effective solutions. By embracing these advancements, pharmaceutical manufacturers can enhance the quality and efficiency of their processes, ensuring the consistent delivery of high-quality, safe medications. Invest in advanced automated visual inspection systems for lyophilized vials to optimize your manufacturing process and guarantee superior product quality.
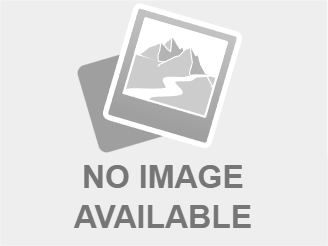
Featured Posts
-
Tom Cruises Dating History A Comprehensive Overview
May 11, 2025 -
Celtics Unlikely 40 Point Performances A Double Record Night
May 11, 2025 -
John Wick 5 Hope Vs Reality Keanu Reeves Weighs In
May 11, 2025 -
The Humanitarian Crisis In Gaza Examining The Effects Of The Israeli Blockade
May 11, 2025 -
Addressing Challenges In Automated Visual Inspection Of Lyophilized Vials
May 11, 2025